Get uniform results with professional plastic extrusion techniques
Get uniform results with professional plastic extrusion techniques
Blog Article
Understanding the Fundamentals and Applications of Plastic Extrusion in Modern Production
In the realm of contemporary manufacturing, the strategy of plastic extrusion plays an instrumental function. Unwinding the principles of this procedure discloses the real versatility and capacity of plastic extrusion.
The Fundamentals of Plastic Extrusion Process
While it might appear complicated, the principles of the plastic extrusion process are based on reasonably simple principles. It is a production procedure wherein plastic is thawed and then shaped right into a continuous account with a die. The plastic extrusion process is thoroughly used in numerous markets due to its versatility, cost-effectiveness, and performance.
Different Sorts Of Plastic Extrusion Strategies
Building upon the fundamental understanding of the plastic extrusion procedure, it is essential to explore the different strategies associated with this manufacturing approach. The two primary methods are profile extrusion and sheet extrusion. In account extrusion, plastic is melted and developed right into a continual profile, usually made use of to create pipelines, rods, rails, and window structures. In comparison, sheet extrusion creates large, flat sheets of plastic, which are normally further processed right into items such as food product packaging, shower curtains, and auto components. Each strategy calls for specialized machinery and precise control over temperature and stress to ensure the plastic maintains its shape throughout cooling. Understanding these methods is vital to utilizing plastic extrusion successfully in modern manufacturing.
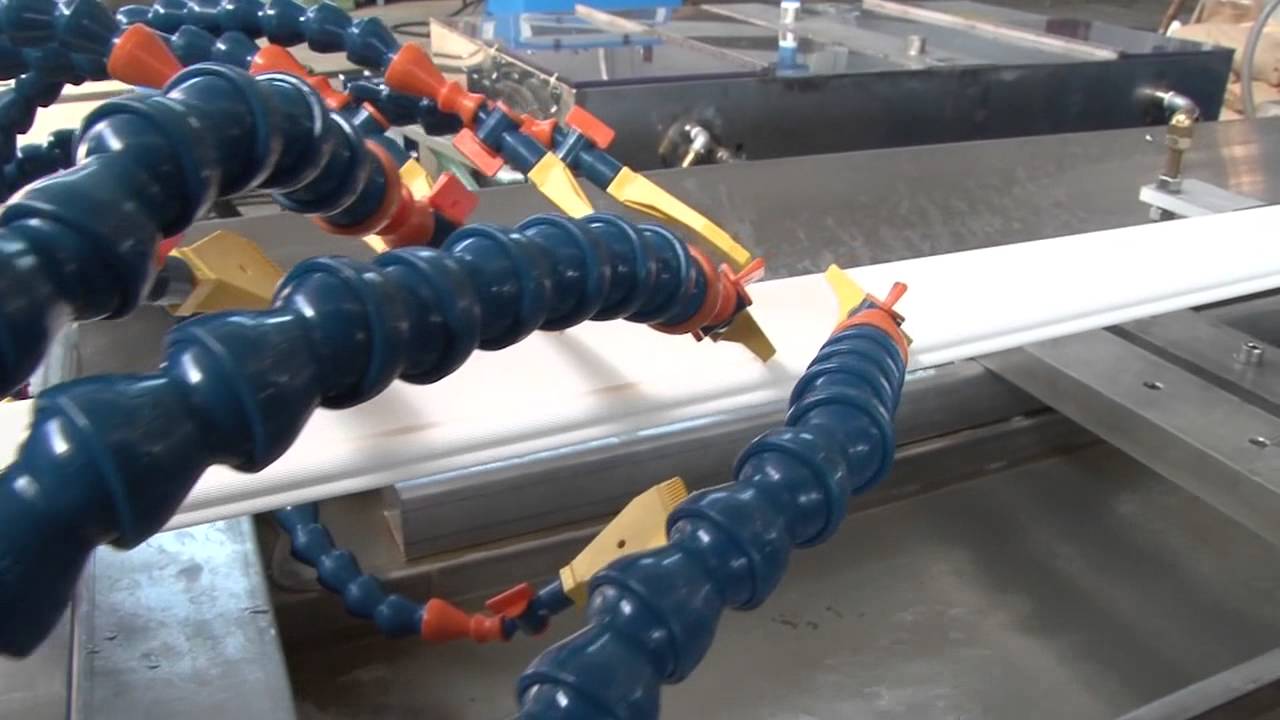
The Function of Plastic Extrusion in the Automotive Industry
An overwhelming bulk of components in contemporary automobiles are products of the plastic extrusion process. This procedure has revolutionized the automotive sector, transforming it into a more reliable, affordable, and adaptable manufacturing field. Plastic extrusion is primarily used in the production of different auto components such as bumpers, grills, door panels, and control panel trim. The procedure offers an uniform, regular output, making it possible for makers to produce high-volume components with excellent accuracy and marginal waste. The agility of the extruded plastic parts contributes to the general reduction in vehicle weight, improving fuel efficiency. Moreover, the toughness and resistance of these parts to heat, cool, and impact enhance the long life of cars. Hence, plastic extrusion plays a pivotal function in automotive production.
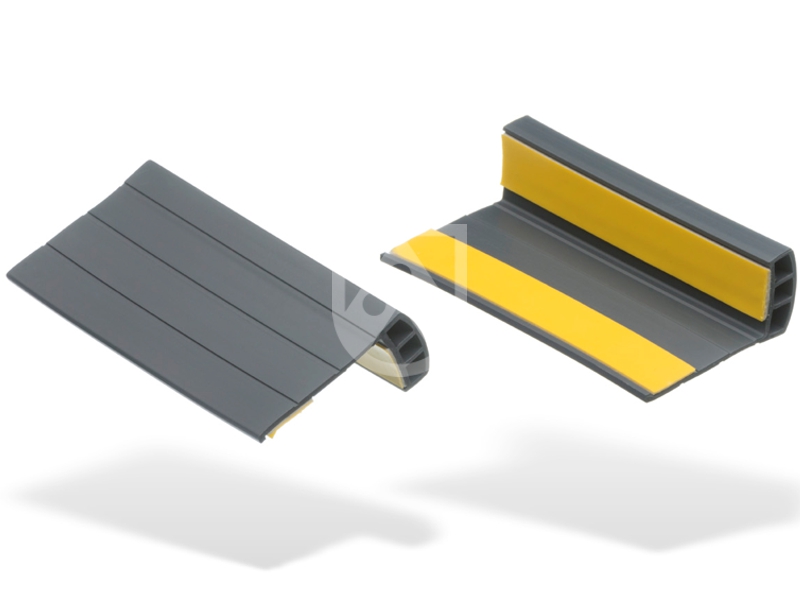
Applications of Plastic Extrusion in Durable Goods Production
Beyond its considerable influence on the automotive market, plastic extrusion confirms equally efficient in the realm of consumer goods making. This procedure is critical in developing a vast range of items, from food packaging to home appliances, playthings, and also clinical devices. The flexibility of plastic extrusion enables producers to make and create intricate sizes and shapes with high accuracy and efficiency. Due to the recyclability of several plastics, squeezed out elements can be reprocessed, decreasing waste and price (plastic extrusion). The adaptability, versatility, and cost-effectiveness of plastic extrusion make it a recommended option for numerous durable goods makers, adding considerably to the market's development and technology. Nonetheless, the ecological implications of this prevalent usage require mindful consideration, a topic to be discussed additionally in the subsequent area.
Environmental Impact and Sustainability in Plastic Extrusion
The pervasive use plastic extrusion in making welcomes scrutiny of its environmental implications. As a procedure that frequently uses non-biodegradable products, the ecological influence can be significant. Energy intake, waste manufacturing, and carbon discharges are all issues. Market improvements are boosting sustainability. Effective equipment minimizes power use, while waste administration systems recycle scrap published here plastic, lowering resources needs. In addition, the growth of naturally degradable plastics uses a more environmentally pleasant alternative. Despite these renovations, additionally development is needed to mitigate the environmental footprint of plastic extrusion. As culture leans in the direction of sustainability, manufacturers must adjust to stay feasible, emphasizing the importance of continual study and innovation in this field.
Conclusion
In final thought, plastic extrusion plays a crucial function in contemporary production, especially in the vehicle and customer items sectors. Understanding the fundamentals of this process is essential to enhancing official site its advantages and applications.

The plastic extrusion process is thoroughly utilized in different markets due to its effectiveness, flexibility, and cost-effectiveness.
Building upon the fundamental understanding of the plastic extrusion process, it is necessary to discover the different techniques entailed in this production method. plastic extrusion. In comparison, sheet extrusion produces large, level sheets of plastic, which are typically more processed into items such as food packaging, shower curtains, and auto components.A frustrating majority of components in modern-day vehicles are items of site the plastic extrusion procedure
Report this page